Challenge
More and more companies operating in the Manufacturing sector feel the need to optimize their production processes, strengthening the synergy between manual and automated work.
The client, a key player in the European bathroom furniture market with a strong vocation for excellence and innovation, decided to start an explorative Proof of Concept with Qintesi.
Prototype aims:
- improve the timing and reliability of the semi-automatic packaging process, which is currently not fully exploited, with a particular focus on the packaging of one of the company’s flagship products: the shower enclosure.
- identify the optimal production mix with which to feed the packaging lines, ensuring as high and constant a product flow as possible, depending on the availability and priority of the products to be packaged.
Solution
After some assessment sessions, the development team decided to decouple the problem into two parts:
- Cluster products into homogeneous classes and estimate their average packing times.
- Develop an optimization algorithm which is able to simulate different lines occupancy scenarios, to identify the most efficient product mixes.
The second phase of the problem proved particularly challenging because of the need to define the scheduling of loading stations operated by physical operators in consideration of several factors:
- the capacity of the various packaging lines and individual downstream logistics facilities (warehouse, etc…),
- the volume of production carried out by automated machinery-a variable number whose scheduling is known only with limited advance and which affects the level of line occupancy,
- the availability and skills of the operators responsible for packing,
- the activation times of individual loading stations,
- the variability of line-edge composition, the priority of present orders, and the need to estimate with reasonable accuracy the availability of products to be packed.
The computational cost, the complexity of the process, and the need for low-latency responses prompted the team to opt for a Cloud solution, drawing on the services made available by the Google Cloud Platform, in particular Vertex AI: a platform for training and deploying a wide range of Artificial Intelligence models, through which the algorithm then shared with the Client was developed.
Risults
- Implementation of dynamic and robust scheduling for shower box packing
- Increased operator productivity by 30% compared to a "typical" day
- Achievement of the nominal packing target of the lines
- Meeting all production constraints required by the Customer (line capacity, operator presence and their skills, priority and availability of boxes to be packed)
Quote
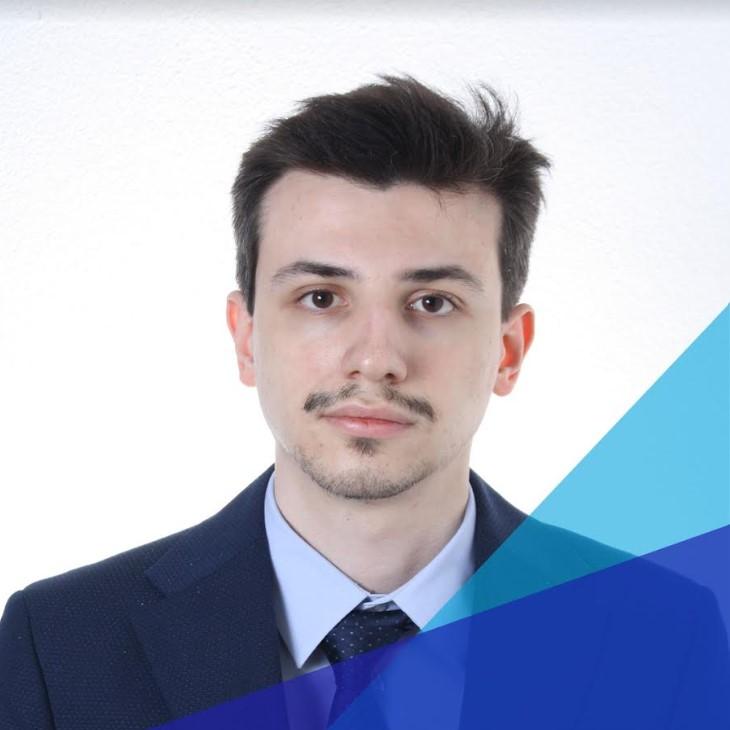
Le informazioni contenute in questo documento sono di proprietà.
Copyright © 2014 Qintesi S.p.A. Tutti i diritti riservati.